この記事では、Autodesk Fusion 360 でアルミ切削加工キーボードケースを設計する手順について説明します。 Fusion 360 そのものについては、扱いやすいソフトウェアでありチュートリアル記事が豊富にありますので、ここではキーボードケース設計に必要なポイントを中心に説明をしていきます。
本記事は、キーボード #1 Advent Calendar 2020 の 16 日目の記事です。前日はきせのんさんの 「2020年キースイッチ関連の回顧」 、翌日は Pekaso さんの記事です。
はじめに
日本の自作キーボードコミュニティでは、ケースの構造として基板をアクリルやFR4のプレートで挟むサンドイッチ構造が主流となっています。この構造は、比較的容易に設計できることや、安価に製造できるなどのメリットがあります。
一方、海外のカスタムキーボードは、アルミ切削加工でつくられたケースが主流です。アルミでつくられたケースは剛性が高く、適切な構造を選択すれば良好な打鍵感や打鍵音を得ることができます。しかしながら、設計は複雑になりがちで、製造のコストが高いという難点もあります。
よりよいキーボードを目指すのであれば、 3D CAD によるケース設計を避けて通ることはできません。この記事が、アルミ切削加工に興味はあるけれど、なかなか手を出せなかったという人に向けて、そのハードルを下げることができれば幸いです。
プロダクト構想
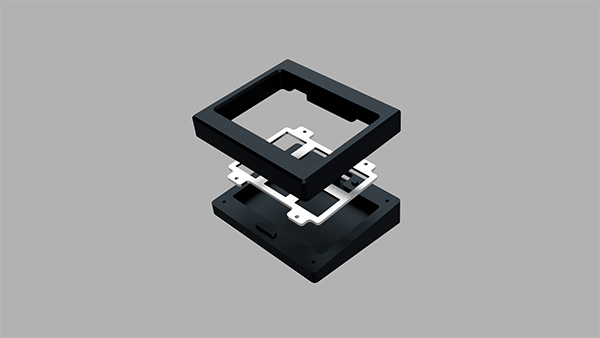
まず、どんなキーボードにするか検討しましょう。チュートリアル記事ですので「オーソドックスな仕様、かつ必要な構造を最小限のサイズで説明したい」と考えると 6 キーのマクロパッドがよさそうです。そこで仕様を下記のようなものとし、プロジェクトを RK6 と名付けます。
- Cherry MX 互換スイッチ対応
- トップマウント
- 6キー(2行3列)
- USB-C コネクタ
このような仕様ですので、ケースの部品はトップケース、プレート、ボトムケースから構成されます。プレートはトップケースに固定され、トップケースとボトムケースはネジ止めされるようにします。
知っておきたいこと
設計にとりかかる前に、前提知識がいくつか必要になりますので、簡単に説明をします。
切削加工について
切削加工は、コンピューター制御(CNC)機能を搭載したマシニングセンターと呼ばれる工作機械で行なわれます。フライス盤といってもイメージがつかないのであれば、 YouTube などで動画をみると良いでしょう。
- https://youtu.be/LOxbk9rulyg (音量注意)
マシニングセンターでの切削加工では設計上の制約が生まれます。マシニングセンターをつかって、どのように切削加工をするのかという解説記事がありますので、目を通してみてください。どの方向からどう削るのかをイメージすると、加工できない形状がどのようなものか、いつ「段取り作業」が発生するのかなど理解することができます。
切削加工の費用について
マシニングセンターは高額な工作機械ですし、簡単に扱えるものではありません。そのため、切削加工は工場に発注をすることになります。注意していただきたいのは、そういった工場は基本的に個人向けのサービスではないということです。営業担当者がいて、見積をもらって、発注をするというスタイルになります。
試作で一点物のを発注すると高くつきます。サイズや加工の複雑さにもよりますが、通常のキーボードサイズであれば、最低でも5万円はかかるものと考えてください。これは個人にとっては少なくない金額です。
ところが、法人相手のビジネスでは、数万円の案件というのは効率的な案件ではありません。試作を受注するのは、ある程度の規模の発注がその後あることを期待して、ということもあるでしょう。あまり萎縮をすることもないのですが、そのような事情は念頭に置いておく必要があります。
PCBについて
その他、ケースにあわせた PCB もつくることになります。自作キーボードでよくつかわれるマイコンボードである Pro Micro を利用すると設計上の大きな制約になってしまいますので、直接基板に電子部品を実装するのがよいでしょう。今回、 PCB 設計については説明しませんので、下記の記事を参考にしてください。
なお、PCBの製造時にアセンブリサービスまで頼むと、だいたい数万円がかかります。この費用も見込んでいてください。自分で手はんだ作業をするというのもいいのですが、利用する電子部品やフットプリントに制約がでてしまいます。手はんだ作業はミスをしやすいですし、そして何より面倒です。
Fusion 360 による設計
それでは、いよいよキーボードケースの設計をしていきましょう。とはいえ、キーボードケースの設計に決まった手順はありません。トップビューから設計する人もいれば、サイドビューから設計する人もいます。この記事での手順はあくまでも一例にすぎません。私は最初から完全なものを目指さずに、デザイン履歴機能をつかってインクリメンタルに設計していくのが好みです。みなさんもこの記事を参考に、自分なりのスタイルを見付けてみてください。
トレイ状のケースをつくる
最初に図面のようなトレイ状のケースをつくります。トップケースとボトムケースは別々のデザインとして作成し、アセンブリ機能で組み合わせます。早めに組み合わせを確認することで、全体のバランスや干渉をチェックすることができます。
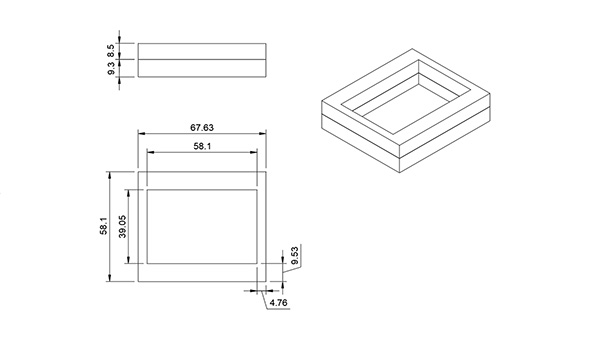
内寸と外寸の大きさはキーピッチ(19.05mm)をもとに設計していきます。幅(W)は3列ですので、19.05 * 3が基本のサイズになります。 0.475mm * 2 を足しているのは、両端のスペースです。同様に奥行(D)も計算します。
- 内寸
- (W) 58.1mm = 19.05 * 3 + 0.475 * 2
- (D) 39.05mm = 19.05 * 2 + 0.475 * 2
外寸は、それに側面の厚さを足したものになります。プレートをネジ止めするスペースを考えて、手前と奥側は厚めにとることにします。計算が楽になるので、手前と奥は 19.05mm の 0.5 倍、横側は 19.05mm の 0.25 倍の厚さにします。
- 外寸
- (W) 67.625mm = 19.05 * 3 + 0.475 * 2 + 19.05 * 0.25 * 2
- (D) 58.1mm = 19.05 * 2 + 0.475 * 2 + 19.05 * 0.5 * 2
ケースの高さ
次は、ケースの高さ(H)について考えていきましょう。Cherry MX のデータシート をみるとキースイッチのハウジングの高さは 11.6mm です。ちょっとだけ余裕をみて 12mm と考えましょう。ボトムハウジングの高さは 5mm ですので、 7mm(12mm - 5mm)がトップハウジング部分の高さです。これにプレートの厚さである 1.5mm を足したのが、トップケースの基本の高さになります。
- トップケース
- (H) 8.5mm = 12 - 5 + 1.5
ボトムケースの高さは、ボトムハウジングの高さ 5mm と足の高さ 3.3mm 、これにクリアランスとして 0.5mm を足し、プレートの厚さである 1.5mm を引いたものになります。外寸は、底の厚さを 2mm とって、 9.3mm です。
- ボトムケース内寸
- (H) 7.3mm = 5 + 3.3 + 0.5 - 1.5
- ボトムケース外寸
- (H) 9.3mm = 5 + 3.3 + 0.5 - 1.5 + 2
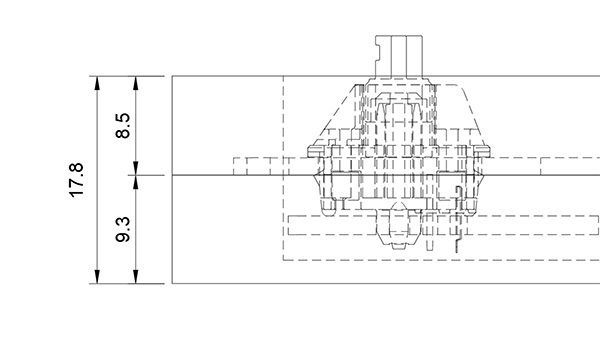
文章で書き起すとややこしく感じますが、プレートの底面の高さでケースを分割するイメージを持つと、すっきりと理解できます。それから、タイピングアングルを調整しましょう。側面にスケッチを作成し、好きな角度をつけます。個人的な好みは 7 度くらいです。
プレート部分の設計
トップケース側では、プレートを固定するための切り欠きをつくります。切り欠きのサイズは、幅が 10.1mm くらい、奥行は枠幅の半分 4.7625mm 、高さがプレートの 1.5mm にします。長方形の中心に M2 3mm のネジ穴をつくります。
- トップケース切り欠き × 4
- (W) 10.1mm = 5.05 * 2
- (D) 4.7625mm = 19.05 * 0.25
- (H) 1.5mm
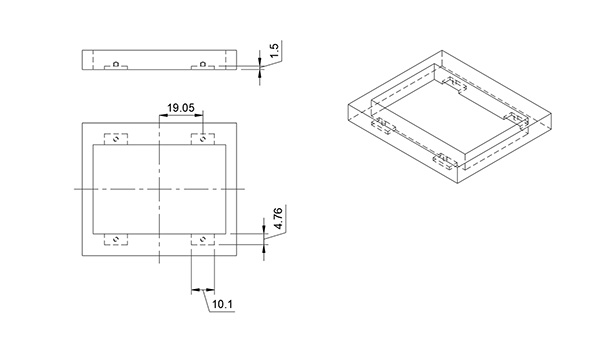
プレートは、 Keyboard Layout Editor で作成した JSON をもとに ai03 - Keyboard Plate Generator を利用して DXF ファイルを生成します。この DXF ファイルをスケッチに挿入し、厚さの 1.5mm 分だけ押し出しておきます。このプレートにタブのような出っぱりをつくって、トップケースに固定をしていきます。
タブ部分はケースのクリアランスである 0.475 を引き継ぐことにします。幅はトップケース側切り欠きの 10.1mm から 0.475 * 2 を引いた 9.15mm にします。奥行は 4.7625mm にプレートとケースの隙間である 0.475mm を足したうえで、プレートと切り欠きの隙間の 0.475mm を引きます(つまり、相殺されます)。そのうえで、 2mm の穴をつくります。穴の位置はタブの中心から外側に 0.475mm だけずれていますので、注意してください。
- タブ × 4
- (W) 9.15mm = 10.1 - 0.475 * 2
- (D) 4.7625mm = 19.05 * 0.25 + 0.475 - 0.475
- (H) 1.5mm

ここまでできたら、アセンブリを確認しましょう。干渉部分が無いか検査機能で確認します。また、穴の位置にずれなど無いかも確認します。
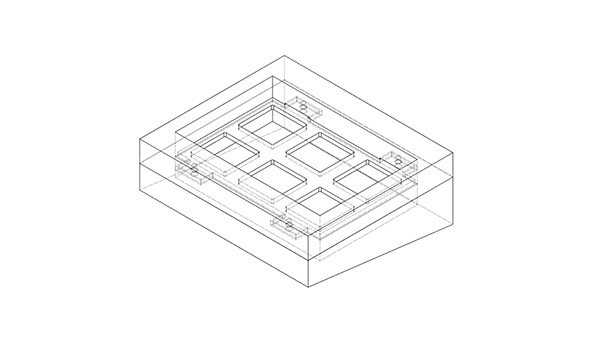
これでプレート部分は完成と言いたいところですが、このままだとネジ止めするときに、ネジ頭部が干渉してしまいます。そこで、 1.8mm ほどトップケースを押し出し、その分ボトムケースを切り取るという調整を行ないます。
トップケースとボトムケースのネジ穴をつくる
トップケースとボトムケースをねじで締結するために、トップケースとボトムケースにネジ穴をつくっていきます。そのままボトムケース側にネジ穴を開けるだけではネジ頭部が飛び出してしまいますし、下穴が長くなりすぎてしまいますので、ザグリ加工をします。ザグリ加工とは、ネジ頭部が底部から突き出ないように穴を開ける加工のことです。
天面からオフセット平面をネジ下穴径の 1.5 倍である 3mm で作成します。いつも 廣杉計器の M2 ネジをつかっているので、直径 4mm ほどの円筒で切り取りをして、円筒の底面に M2 3mm のネジ穴をつけます。それから、トップケースの同じ位置にも M2 3mm のネジ穴をつけます。
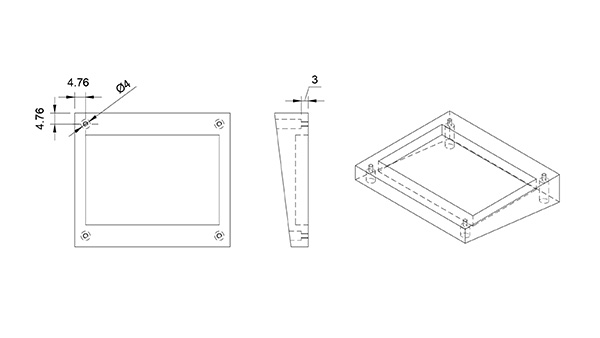
USB-C 部分の設計
次に USB-C コネクター部分の設計をしていきます。 UCB-C コネクターには TYPE-C-31-M-12 を採用しています。コネクターの外形は (W) 8.94mm × (H) 3.21mm になるので、 0.5mm のクリアランスを含めたサイズがコネクター部分のサイズになります。
- (W) 9.44mm = 8.94 + 0.5
- (H) 3.71mm = 3.21 + 0.5
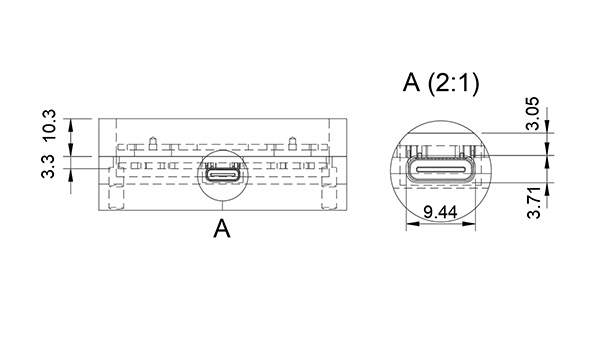
UCB-C コネクターはPCB底面に実装されるので、ボトムケースの天面から PCB 底面までの距離を計算しましょう。プレート底面からプレートの厚さ -1.5mm がプレート天面の高さです。プレート天面から PCB 天面までは 5mm 、そこから PCB の厚さが 1.6mm ですので、それが PCB 底面の高さです。プレート用のネジ頭部のために 1.8mm ボトムケースを低くしていたので、その分も忘れないようにします。さらに、クリアランスの 0.25mm 分も調整します。
- 3.05mm = -1.5 + 5 + 1.6 - 1.8 - 0.25
ボトムケース天面から 3.05mm の高さに 9.44mm * 3.71mm の穴をつくればよいということがわかりましたので、側面にスケッチをつくって切り取りをします。さらに、 1.5mm のフィレットを指定しておきます。
PCB 底面に 3.21mm の高さを持つ UCB-C コネクタが実装されるので、ボトムケース天面から 6.51mm の高さになります。 PCB は凸型になるますので、飛び出した部分が収まるように 1mm を残して奥側の壁部分を切り取ります。
- 7mm = (-1.5 + 5 + 1.6 - 1.8) + 3.21 + 0.49
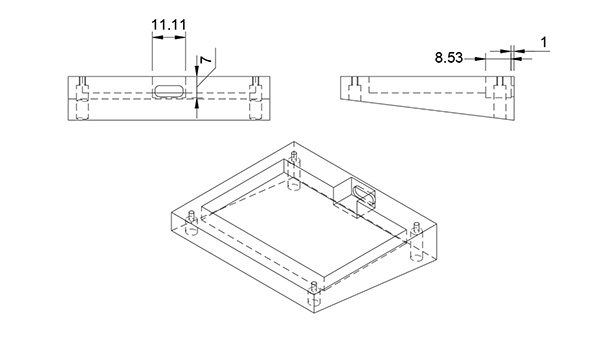
位置合わせガイド
だいたい形ができてきたので、トップケースとボトムケースを組み合わせるときの位置合わせガイドをつけます。線対称にすると、前後を反対にしても合わせることができるので、線対称でない配置を選びます。奥側に 3mm * 3mm 、手前側に 3mm * 12mm のガイドを作成します。ボトムケース側を 2mm ほど押し出して、トップケース側を 2mm ほど切り取ります。
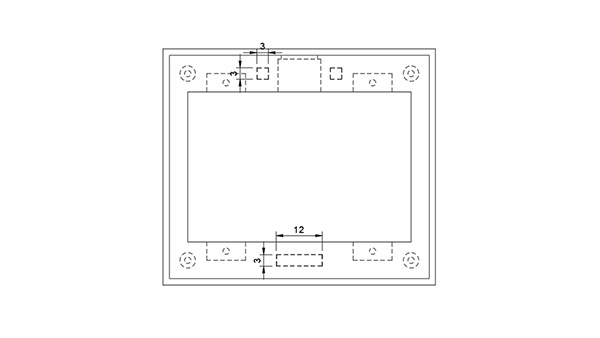
フィレット加工、面取り加工
最後にフィレット加工、面取り加工をします。どういう部分で隅 R が必要になるかということは、最初に紹介したサイトなどを再度確認してみてください。真上から円筒形のエンドミルで削っていくイメージを持つと、想像がしやすいかと思います。
フィレットのサイズは、外側を半径 2mm 、内側を半径 1.5mm にしています。フィレットのサイズは、切削に利用するエンドミルの直径と突き出し量とが関係します。細いエンドミルでは、深くまで削ることができません。エンドミルの突き出し量、つまり深さはエンドミルの直径の 5 倍くらいまでという目安があるようです。とはいえ、工場によっては加工の都合によって、もうちょっと大きめの R にしたいという修正案を提案されたりします。ある程度、余裕のある数字で設計するのがよいでしょう。
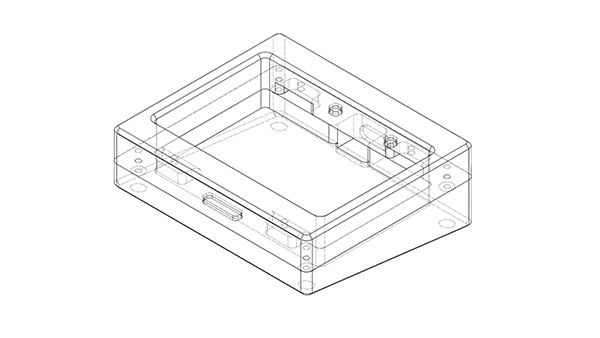
以上で、ケースの設計は完了です。
製造について
設計したケースを工場に発注するには、要求仕様をまとめて、その仕様で製造してくれる発注先を探すことになります。本格的に製造するということであれば、 Alibaba で地道に工場を探すのが一番なのですが、かなり手間がかかります。
そこで、今回は 3D Hubs で見積をとってみます。このサービスはオンラインで金属切削加工を依頼できるサービスで、 step ファイルをアップロードするだけで発注ができます。見積も簡単に出してくれますし、加工できない形状があれば自動でチェックしてくれますので、ざっくりと設計に問題がないか、どれくらいの費用になるかということを知りたいのであれば、まず利用してみるのがよいでしょう。
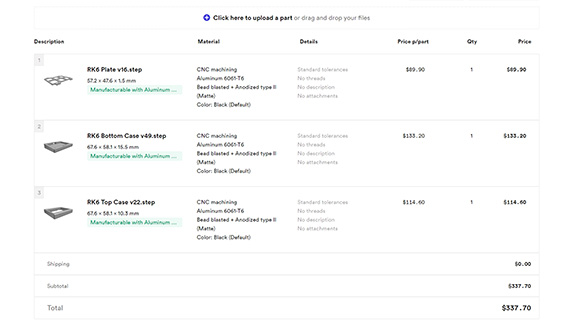
はい、いいお値段ですね……。プレートの価格が少し高いので、別のところに発注すればもう少し安くできるかなあという感想です。
3D プリンターでプロトタイプを出力して、うまくいくかどうかを確認した方がよいのではないかという意見もあるかもしれません。しかし、キーボードのサイズとなるとそのまま出力するのが難しいことや、それなりの費用と時間がかかること、造形の精度や制約がまったく違うことなどを考えると、あまりメリットを感じないというのが正直なところです。
おわりに
本記事では、 Fusin 360 でアルミ切削加工キーボードケースを設計する手順を解説しました。ソフトウェアの細かい操作手順などについては解説はできませんでしたが、大まかな流れについては理解いただけたのではないでしょうか。
とはいえ、今回設計したのは Minecraft でいえば豆腐建築に近いキーボードケースです。いくつもの改善点があります。たとえば、ボトムケースのザグリ部分が深すぎて、ドライバーが入りにくい形状になっています。また、USB-Cを接続する部分はもうちょっと隠した方がよいかもしれません。トップケースとボトムケースの繋ぎ目も気になります。それから、最近では単純なトップマウントよりも優れた構造が提案されていますので、そういった設計を取り入れる必要もあるでしょう。
重要なのは、多くの優れたカスタムキーボードから学ぶことです。自分でキーボードを設計するようになると、キーボードの各所に設計者の意図や工夫が込められていることを理解できるようになります。そして、そのキーボードを使い込むことで、その意図や工夫がどのような効果をもたらしているかを知ることができます。カタログスペックやタイピング動画だけでは学ぶことができない部分です。
この記事が、皆さんにとって、よりキーボードへの理解を深めるきっかけになれば幸いです。